The Impact of PVC Stabilizers on Product Performance
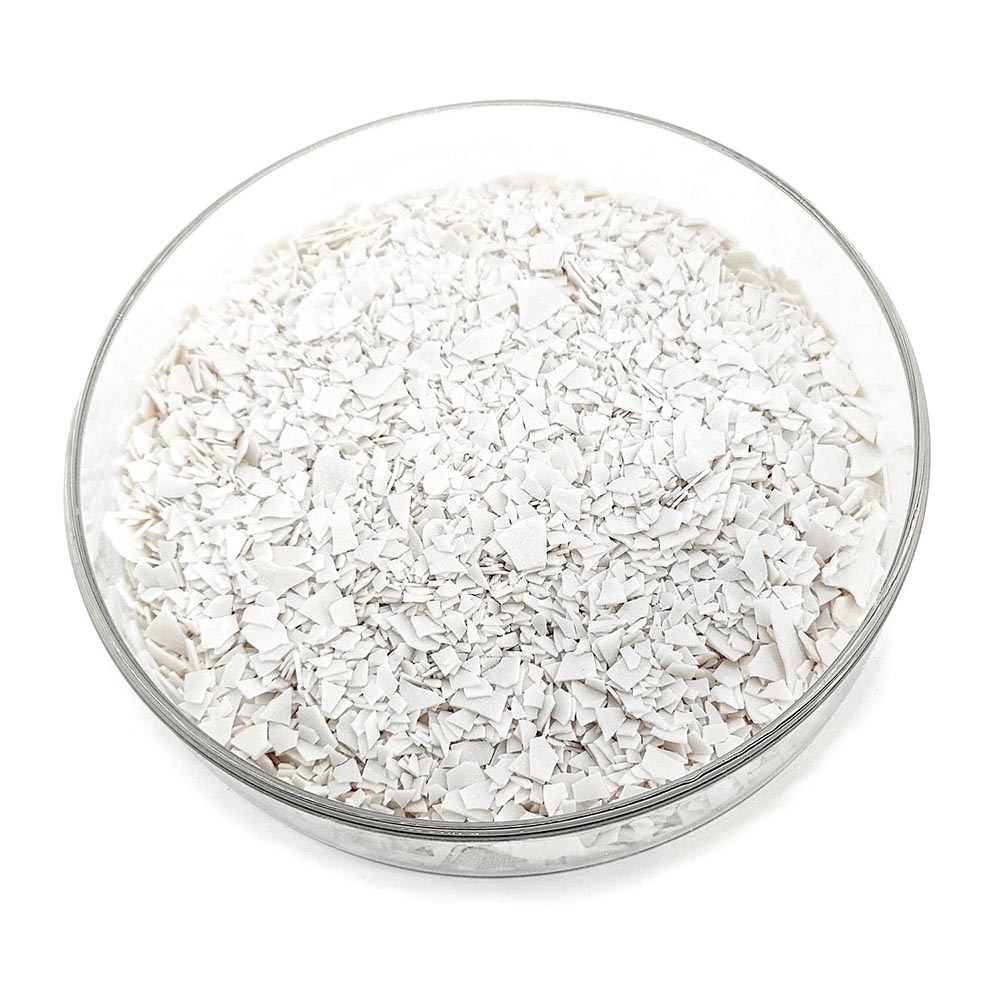
PVC stabilizer
Polyvinyl chloride (PVC) is a versatile and widely used plastic, found in everything from construction materials to consumer goods. However, PVC is inherently unstable when exposed to heat and light, which can lead to degradation, discoloration, and loss of mechanical properties. This is where PVC stabilizer come into play, playing a crucial role in enhancing the performance and longevity of PVC products.
What Are PVC Stabilizers?
PVC stabilizers are additives used to prevent the degradation of PVC during processing and throughout its lifecycle. These stabilizers work by neutralizing hydrochloric acid released during the degradation process, replacing weakened carbon-chlorine bonds, and preventing oxidation. The most common types of PVC stabilizers include:
Lead-based Stabilizers: Historically used but now largely phased out due to environmental concerns.
Calcium-Zinc Stabilizers: Widely used due to their non-toxic nature.
Tin Stabilizers: Known for their effectiveness in providing heat stability.
Organic Stabilizers: Increasingly popular due to their environmental benefits.
Effects on Product Performance
Thermal Stability: One of the primary functions of PVC stabilizer is to enhance the thermal stability of PVC products. By preventing thermal degradation, stabilizers ensure that PVC maintains its structural integrity and performance even at high temperatures. This is particularly important in applications such as automotive interiors and electrical cables, where heat resistance is crucial.
UV Resistance: PVC products exposed to sunlight can degrade due to UV radiation. Stabilizers help in maintaining the color and physical properties of PVC when exposed to UV light, making them ideal for outdoor applications like window profiles and roofing materials.
Mechanical Properties: Stabilizer contribute to maintaining the mechanical strength of PVC products. Without stabilizers, PVC can become brittle and prone to cracking. By preserving the polymer’s molecular structure, stabilizers ensure that PVC products remain durable and reliable.
Chemical Resistance: PVC stabilizers enhance the chemical resistance of PVC products, allowing them to withstand exposure to acids, bases, and other corrosive substances. This makes PVC suitable for use in chemical processing plants and plumbing systems.
Aesthetic Appeal: Stabilizers prevent discoloration and maintain the aesthetic appeal of PVC products. This is particularly important in consumer goods and packaging, where appearance plays a significant role in product acceptance.
Applications Across Industries
Construction: In the construction industry, PVC stabilizers are essential for products like pipes, window frames, and siding. They ensure that these products can withstand harsh environmental conditions and maintain their performance over time.
Automotive: In automotive applications, stabilizers help PVC components resist heat, oxidation, and chemical exposure, ensuring longevity and reliability.
Electrical: For electrical cables and insulation, stabilizers provide the necessary thermal and UV resistance to ensure safety and durability.
Healthcare: In the healthcare sector, stabilizers are used in medical devices and packaging to ensure that PVC products remain safe and effective throughout their use.
Conclusion
PVC stabilizers are indispensable in the manufacturing and application of PVC products. By enhancing thermal stability, UV resistance, mechanical properties, chemical resistance, and aesthetic appeal, stabilizers ensure that PVC remains a reliable and versatile material across various industries. As environmental concerns continue to shape the industry, the development and use of non-toxic and sustainable stabilizers will be crucial in maintaining the balance between performance and environmental responsibility.
Tap here to order from our products